一、前言
山西河坡发电有限责任公司100MW机组制粉系统" title="制粉系统">制粉系统的排粉机原采用入口挡板调节风量,并且为减小三次风量,排粉机入口管道还采取了缩口(Ф1200管道缩为Ф800管道)及增加小挡板的措施,浪费了大量的电能。为降低能耗,经北京利德华福电气技术有限公司专业技术人员多次分析讨论后认为对排粉机电动机进行变频改造是可行的,对制粉系统的负压" title="负压">负压形成及三次风影响不大,因此决定在4#炉排粉机进行高压变频改造。2004年11月22日开始准备材料,DCS系统增加变频标签,下载软件,2004年12月8日土建开工,2005年4月1日开始全面调试,2005年4月7日一次投运成功,节能效果良好。
二、改造情况介绍
1.原设备情况
山西河坡发电有限责任公司4#炉排粉机设备技术参数:
1)排粉机数量:2台
2)排粉机参数:

配套电机参数:
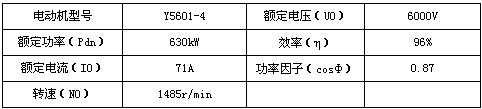
3)运行参数:单台排粉机风量48000 m3/h,年运行时间5850小时,工频运行时电动机平均电流Ig40A。
4)电价:单位成本电价:0.24元/kWh
2.改造后的设备情况
1)HARSVERT-A06/080高压变频调速系统" title="调速系统">调速系统如图1,技术参数如下表:

HARSVERT-A06/080设备参数

2)变频调速系统主回路介绍,如图2
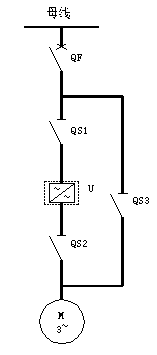
图2:变频调速系统主回路
系统由变频器" title="高压变频器">高压变频器和旁路柜两部分组成,图2中所示的QS1、QS2、QS3均包含在旁路柜中。QF、M为原有设备。
该系统具备手动工/变频切换功能。QS2和QS3不能同时闭合,在机械上实现互锁。变频运行时,QS1和QS2闭合,QS3断开;工频运行时,QS3闭合,QS1和QS2断开。
3、排粉工艺介绍,如图3
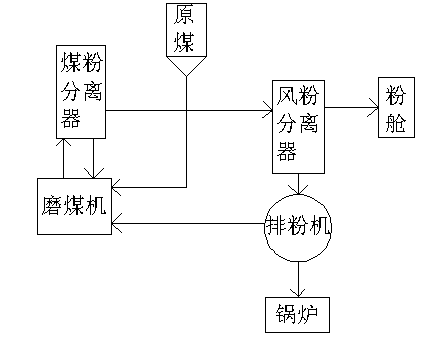
图3:排粉工艺流程图
排粉风机在制粉系统中装在球磨机,粗粉分离器、细粉分离器之后,保证原煤在球磨机内同来自空气预热器的热风和排粉机出口的再循环风混合,将原煤干燥,并研磨成煤粉,而煤粉随排粉机所产生的负压气流,经细粉分离器把风、粉分开,煤粉落入煤粉仓中贮存,剩余气体内含有5~10%的风、粉混合物,作为三次风经排粉风机出口送入炉膛或作为一次风与给粉机落下的煤粉排入一次风箱混合送入炉膛。通过上述流程介绍我们可以看出,在制粉系统中排粉机主要为系统提供负压。在对排粉机进行变频改造后通过将排粉机入口风门全开,同时适当调节出口风门,完全可以满足为制粉系统提供负压的需要并且不对三次风造成影响。
三、排粉机节能效果
1)、单台工频功耗计算:
Pd:电动机功率;ηd:电动机效率;U:电动机输入电压;I:电动机输入电流;cosФ:功率因子。
计算公式:Pd= ×U×I×cosФ
单台工频功耗:Pd= ×U×I×cosФ=1.732×6V×40A×0.87=361.64kW(包括管道缩口及挡板节流损失)
2)单台变频功耗计算:
通过流体力学的基本定律可知:风机、泵类设备均属平方转矩负载,其转速n与流量Q,压力H以及轴功率P具有如下关系:Q∝n,H∝n2 ,p∝n3;即,流量与转速成正比,压力与转速的平方成正比,轴功率与转速的立方成正比。
将现场运行数据带入 = 公式(Q1是实际排粉机风量,Q0是额定排粉机风量,P0是风机的额定功率),
可得变频工耗:P1=144.90kW
变频器网侧功耗:Pb= = =150.94 kW
3)单台节电率计算:
单台节电率:(ΔP/Pd)×100%=(210.7/361.64)×100%=58%
4)单台实现节电率计算:
变频运行时电动机平均电流Ig17A。
实际节电率:1-(Ib/Ig) ×100%=1-(17/40)×100%=57.5%
5)变频调节改造后的效益:
年节约电量=排粉机台数×单台变频节电率×单机工频功率(KW)×年运行小时=2×57.5%×361.64×5850=2432933.1(KWh)按0.24元/KWh计算,每年可节约电费58万元。
按照2004年二期发电量1439505600KWh计算,二期厂用电率可下降0.17%。
目前排粉机入口挡板虽已开至100%,但风机入口管道仍为缩口处理,我们计划利用检修机会将该缩口及小挡板进行改造,进一步减小节流损失,使变频改造效果进一步扩大。
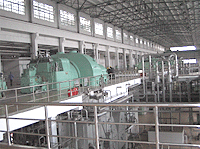
图4:发电机组
图5:操作控制板盘
四、变频改造带来的其他效益
1)由于排粉机属于频繁启动设备,采用变频调节后,高压开关常合,极大地延长了检修周期。
2)变频调速可实现软启动,延长了电机及风机的使用寿命。
结束语
对排粉机进行变频改造,在国内还是第一次进行,河坡电厂变频改造的成功经验,为电力行业中储式制粉系统高压电机改为无级调速的变频控制奠定了很好的基础。今后会有越来越多的火力发电厂进行类似改造,我们希望有机会同业内同仁进一步交流变频应用中的经验,共同为建设节约型社会贡献自己的力量。