能够对处在生产阶段的医疗设备进行测试的测试平台,有助于公司管理电子元器件的成本、接入和覆盖范围。
不管各家公司有没有在产品开发阶段对产品进行诊断,也不管它们在生产过程中有没有确保产品质量,但它们都免不了必须要考虑对产品进行测试。因为涉及到诸多变量和特定情况,所以事实上几乎不可能有一种万能的测试策略。例如,考虑到电路板上的微型元器件和高度集成的元器件,对电路板进行测试要求使用富有创造性的新工具和方法。也许这可以解释为什么很多公司,尤其是那些小公司,都很头痛制定测试方案时需要考虑的三大主要要素:成本、接入和覆盖范围。
产品设计公司意识到需要在产品开发阶段有对产品进行测试,但可能对于分配多少资源用于生产阶段的测试存在内部争论。不管存在什么样的争议,最重要的一点是产品测试是少不了的。不管出于什么原因忽略生产测试需求,都不能制定出一个有效的策略。
每次在考虑测试优先权的时候,测试成本的讨论都会成为焦点。产品设计公司要么投资购买昂贵的新款测试设备,要么放弃原本必须进行的测试。现在,产品设计公司有了一种替代方案---一款能将测试开发投资和适用性最大化的测试平台方案。
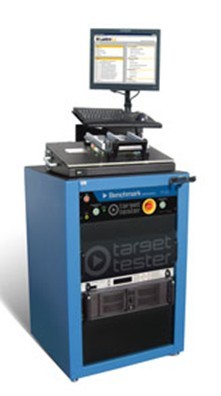
平台方案的优势
大多数OEM和EMS供货商不敢去想购买一套用于测试所有产品的仪器需要多少成本。很多测试开发团队已经发现平台方案是一款具有成本效益并且考虑周到的测试替代方案。
该平台由一系列现成的测试设备组装而成, 可以非常灵活地进行修改,以满足变化的测试要求。测试平台基于一系列供应商提供的仪器架构,可以根据新的(测试)需求进行升级。其中一个例子就是,一款由某个供应商在10多年前开发的测试平台,仍然能够适应新产品和对新产品进行测试。该平台是第三代产品,在新仪表上市之后即随之升级。
OEM,特别是EMS供应商,将采购这类测试平台视作是对架构的理性投资,因为架构未来是能够升级的。测试平台能够对多种产品进行测试,通过重复使用投资资金,节省了大量成本。
平台架构和其固有的灵活标准化可为用户提供一系列好处。
熟悉。因为操作人员可以使用相同的测试方案和接口对多种产品进行测试,所以不要求多重培训方案或证明。大体上来说,一个平台能够提供一个组织范围内的知识库。
重复使用。即便是对新产品或设备进行测试,甚至要求用到更复杂的测试方法,也不必对平台架构进行彻底改造。
缩短开发日程。设计人员将会发现,设计概念和生产之间的时间间隔将被缩短。测试开发人员可以更早的着手将平台用于产品的性能和验证试验。
维护。平台有现成的的备用零件,能够节省时间和费用。
解决一次性工程费用(NRE)问题。NRE支出一直是产品开发的祸端,并且还有很好的理由。NRE是指针对任一新产品开发一款测试方案所需的开发成本---要确定该产品是否仍然能够赢利,必须考虑NRE成本。若采用平台测试解决方案,则有助于降低NRE测试成本,因为测试平台在对新产品进行测试时,不需要或者仅要求极少的测试平台开发工作。
复制和支持。可用利用库存零部件在几周之内组装完成现货平台,而不用重新开始和搭建一款新的测试仪。将两者对比发现,新款测试仪通常需要8-10周才能完成,而依据平台设计图组装一款测试平台通常只需要4周时间。
对测试持异议
各种各样的利益相关者对特定测试的必要性持有不同的观点。产品研发部主管可能最关心将成本最小化、接受程度,并假定可以牺牲质量。生产部则主要关心是否成功生产-通过测量设备的产量是否达到或超过预期目标值来判定。
对于医疗设备而言,这些观点和苛刻的FDA预期,以及用于获取产品满足关键功能参数的证明掺杂在了一起。只关心成本会导致生产的噩梦,因为没办法生产出一款可靠的产品;而只关心产量可能会重加新产品上市的负担,导致项目在能投放市场之前就已经被枪毙掉了。因此必须由产品设计部和生产部联手合作,找到一个折中的办法。
对于有些公司来说,测试没有附加价值。“如果我们的产品设计上没有问题,那我们就不需要测试,”这是最常见逻辑。这是一个有缺陷的假设。进行测试可以再次确保产品的优良性,并且测试是收集反馈信息的工具,而调整产品生产需要这些反馈信息。测试能揭示因产品设计、材料和生产过程变更所导致的缺陷。
技术正在以极快的速度前进,特别是在产品和电路板设计领域。分立元器件持续缩量,处理器速度持续上扬,面阵列封装的密度增大。依赖定制ASIC开发的产品数量也在不断增长。对产品微型化的需求仍在持续加速。如今,要一步到位地搭建好一个平台也是一件十分具有挑战性的事情,因为电路行业正在由引线元器件向表面贴装元器件转变。
当前迅速发展的技术给产品设计人员制造了重重挑战。因为产品设计人员必须挤出电路板空间用于测试点接入,有时候这被视做真正的挑战。因为电路板越来越小,越来越难给放置测试点。减少单位电路板密度的测试点数量正成为该行业的一个趋势,对产品尺寸和经济方面的考虑推动了这一趋势,但是这种趋势也不是没风险。没准中间某个被去掉的测试点就会导致对某个严重影响设备功能的问题产生错误的诊断。在制定测试策略时,必须对减少测试接入点所带来的影响进行评估。产品有很多种测试方法,但希望每个人都关注成本最低的那种方法—在产品处于制造过程阶段就早点其进行测试。
尽管测试很重要并且产品有测试的固有需求,但市面上现有的大多数(测试)系统价格都太贵。考虑到传统测试系统以及新款测试系统的高成本,虚拟和小公司很难找到合适的测试策略。即便是中型或大型公司也会在事后盾疑,是否值得为了发布某款小批量生产的产品而去做测试投资。因为和大批量生产的产品相比,小批量产品的测试成本在总成本中占到了非常高的比例。
价格昂贵的测试系统极可能压垮开发预算和突破底限。以给医疗产品(例如,植入装置监控器)增加手机功能这一趋势为例。用于手机的测试系统可能十分昂贵,即便有些中等规模公司也不够预算。而那些之前有投资测试设备的公司,则可能发现原有测试设备和最新版操作系统不兼容。信息技术小组总是追逐最新的数据保护方案。
对于负责维护测试系统的人来说,用最新的操作系统和应用程序更新测试系统,意味着新的挑战。要让测试设备能够被反复使用,搭建一个能够支持软件升级的灵活测试平台是必不可少的。
单独、定制测试存在的问题
大概每家公司都有自己的测试策略,不管是设在设备的开发阶段或生产阶段。在执行测试略之前,必须对产品变量,如物理尺寸、测试接入、复杂程度、技术和支持等进行检查。只有全面考虑这些要素才能阐明测试策略。此外还有一些不那么切实但可能同样重要的因素:是否兼容标准、产量预测、简化缺陷检测 、配置要求、数据报告和保管以及封装检验要求。
大多数公司的基本测试策略包括:产品组装之前的板级测试,然后是子装配件测试或多次子装配件测试(适用的话),最后是设备级的功能性测试。对于医疗设备而言,质量压倒一切,所以还要求进行其它测试。医疗设备增加的测试可能包括高电压和绝缘安全测试、产品编程、最终产品配置、特殊功能验证和自动视觉检测。这些附加项和测试成本一起,足以让成本敏感的制造商和生产商绝望,他们觉得定制太贵了。
提倡使用通用测试平台用于每级测试,无须采用单独、定制测试,GE医疗集团就是一个很好的例子。GE医疗护理生命保障解决方案项目主管Wesley Moreau并不赞同使用数目众多的专用定制测试。该公司倒是已经创立一个共享的平台方案。“否则,你就是把很多钱投资到一个一次性使用的系统,这样做不具备成本效益,” Moreau表示。
工作人员问题
不论规模大小,每家公司都必须设立一个测试团队,用于全面地评估开发新款医疗设备所遇到的全部挑战:技术、成本和进度按排。若是由中、小型公司开发产品,那么测试团队的规模可能会受到限制。事实上,考虑到聘请有经验的测试人员需要支付高薪,许多公司迫于压力只好将测试团队压缩减到最小。
有一个替代方案是,将测试开发人员放到制造工厂,或者更多的是雇用合同制造商。一个成功的测试开发团队包括一位项目经理、测试-开发工程师主管、测试开发人员、一名机械设计人员, 一名印刷电路板设计人员和一名质量保证工程师。只有少数OEM有财力在公司内部设立这样一个测试开发团队。因此,大多数OEM可以从雇用了这样一支团队的电子专业制造服务 (EMS)供应商所提供的服务中受益。
平台测试成功案例
GE医疗公司的现货测试平台使用经验,可以供考虑使用平台测试方案的医疗设备公司借鉴。该公司用一个测试平台对四个产品系列所涵盖的多个子装配提供功能性测试解决方案。该测试平台配置了支持这一测试解决方案所必须的全部仪器。据该项目主管Moreau表示,相比专用测试解决方案,估计这一基于平台的解决方案所用资本设备将成本减少了38%。GE医疗公司预计,相比定制解决方案,测试平台方案将测试开发时间缩短了15%。
Moreau表示“平台测试已经帮我们节省成本和减小对楼层空间的需求,以及缩短我们的周转时间”。若在制定决策时需要考虑规划长期策略和商务合作伙伴关系,那么Moreau建议这些公司考虑采用专用的产品测试解决方案。
测试帮助产品稳步打入市场
测试平台方案可以解决有关成本、(测试点)接入和覆盖范围的首要测试矛盾。测试的价值仍需要被认可。尽管生产过程技术取得了前所未有的进步,但也不至于让测试变得一无是处。近年来,技术进步就算没有超越业已跟上制造测试的步伐。的确,制造过程正在突破极限—所以制造过程为什么需要测试来支撑有了更多的理由。
对OEM来说,好消息就是在将其医疗产品推向市场之前,他们不必从头开始,也不用处理漫长的测试开发日程安排,更不会有让他们难以接受的测试成本。最重要的是,因为可以轻松地修改测试平台解决方案,使其可对处在开发阶段或处在生产阶段的具体产品进行测试,这样OEM就可以在整个开发和生产周期内对产品的功能进行评估。
对于理解早期测试必要性的成熟医疗公司以及手头资源不多且经验不足的公司来说,平台测试方案将被证明是一项明智的投资。当然,他们必须首先认同测试是所有成功产品发布的先决条件。