关键字:工业电机 最大效率
RIO架构目前已被用于多款系统中,如EUROelectronics等公司的系统。借助该架构,从产品原型设计到最终机械设备完成,EUROelectronics只用了3个月的时间。
缩短机械设计时间
无刷DC和永磁同步AC电机(PMSM)二者通常组成无刷DC电机(BLDC),其集成式控制非常复杂,是一个挑战。许多机械制造商都缺乏构建嵌入式控制器方面的软硬件设计经验,难以让嵌入式控制器在各种类型的模拟和数字传感器上实时执行闭环控制。
为了缩短嵌入式机械制造商的最终设计时间,本文介绍的方案在CompactRIO产品中集成了某种形式的RIO架构。这种基于FPGA的配置包括基于Virtex-5 LX85到Spartan-3的系统,以及基于Virtex-II 1M门的背板,配合基于PowerPC 603e的处理器,能够满足多种频率和性能需求,如图1所示。

图1 在CompactRIO产品中集成了某种形式的RIO架构
在RIO框架中集成配置软件实用程序和动态I/O重构功能可节约设置时间,而且终端应用编程人员和数字设计工程师还能重复使用有关资源。配置软件能自动检测系统中安装的定制硬件。I/O外设的集成式诊断测试可确保I/O器件正常工作。
如果不安装I/O电路,驱动程序软件及相关API不能适当执行或返回具体器件的故障,就会出现问题。为解决上述问题,软件开发人员通常会创建模拟子例程,临时替代应用中的I/O电路代码。这种方法难以立即开始应用开发,而且几乎不能调试代码。RIO中间件驱动程序架构包括相关功能,可将模拟代码直接集成到函数驱动程序中,从而简化代码的重复使用与故障调试。
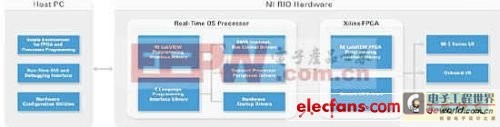
图2 嵌入式中间件软件设计分级图
图2所示为嵌入式中间件软件设计分级图。这种中间件驱动程序和系统服务在成千上万种已经部署的机械设计应用中都证实了自己的功能。并行和多线程安全型嵌入式中间件驱动程序是RIO的有机组成部分。机械制造商可同时从多个线程调用多线程安全型和可再入函数,同时还能确保正常工作,避免阻塞现象,这对并行代码的编写和性能优化都是非常重要的特性。不具备可再入执行功能的驱动程序会影响性能,更糟的是还会导致崩溃。代码必须等其他线程使用完每个函数后才能访问函数。可再入性可避免代码中任何不必要的依赖性。
BLDC和PMSM的定子缠绕方式有别。BLDC的定子旋转时其缠绕方式可生成梯形反电势电压,而PMSM的电压则为正弦曲线。
BLDC的成本高于AC电感电机,但在用高级算法控制情况下其节能性和性能更高。此外,BLDC还具有较高的可扩展性,能满足极高功率和极高速应用的需求。
关键字:工业电机 最大效率
顾名思义,无刷DC电机工作时是不需要电刷的。这就是说,电刷所起的转换作用必须以电子方式实现。定子线圈顺序加电,BLDC电机就能转动了。要计算在某一时刻哪个线圈加电,必须了解定子的位置,这通常可通过在定子中嵌入的三个霍尔效应感应器来检测。综合这三个感应器信号,控制电子产品可确定转换的确切顺序。
由于无刷电机的转子使用永磁而非无源线圈,其本身提供的功率相对于尺寸、重量相当的电感电机而言要高。不过,高效运行的关键在于FPGA控制器。FPGA算法控制的效率高于微处理器。可以使用多种控制系统算法,包括梯形、正弦和场定向算法(FOC)。
梯形或六步控制是最简单同时也是性能最差的方法。就六步转换的每一步而言,电机驱动会在两个线圈之间形成电流通路,而第三个电机不连接。不过,转矩纹波会产生震动、噪声和机械磨损,并大幅降低伺服性能。
FOC也称作矢量控制,能在较高电机速度下提高效率,在正弦控制技术基础上更进一步。FOC相对于其他控制技术而言,单位功率输入可实现最大转矩,而且在负载变化时能精确控制速度,响应速度快。FOC技术通过完美保持定子和转子磁通,即便在瞬态过程也能确保最佳效率。
探讨FOC
了解FOC工作原理的方法之一是在脑海中形成一幅完整的坐标参考系转换过程画面。假设从定子角度来设想AC电机的工作,可以看到,当正弦输入电流施加到定子时,时变信号会产生旋转磁通。转子速度与旋转磁通矢量存在一种函数关系。
现在,再从电机内部来看,假设以等同于定子电流产生的旋转磁通矢量的速度沿离心器运行,在稳定状态下从这个角度来观察电机,可发现定子电流好像为常量,且旋转磁通矢量为固定的。归根结底,希望控制定子电流,以获得所需的转子电流。通过坐标参考系转换,可通过简单的PI控制回路控制定子电流,如DC值。
FOC算法在后台发挥作用,消除时间和速度的依赖性,能直接独立控制磁通量和转矩。通过数学公式(Clarke及Park变换),可将电机的电子状态转换为时间不变性旋转两轴坐标系。
空间矢量脉冲宽度调制(PWM)的高效控制电力电子技术能最大化电机电源电压的利用率,同时最小化谐波损耗。但谐波会在电机铁芯中形成消耗能量的涡流,从而大幅降低电机效率。
最重要的是,设计人员既可对AC电感与无刷DC电机采用FOC技术,以提高其效率和性能,也可将该技术应用于现有电机,升级控制系统。事实上,设计人员可通过FOC等矢量控制技术来改进AC电感电机,实现类似于伺服电机的性能。
FPGA解决FOC面临的挑战
实施FOC需要功能强大的计算器件。针对上述要求,FPGA无疑是电机控制的最佳选择。FOC系统必须持续以10kHz~100kHz的速度重复计算矢量控制算法。此外,还需在不影响控制算法时序的情况下并行执行高速PWM输出等其他IP模块。利用FPGA自身的并行执行功能和硬件可靠性,FPGA能以高达数十万赫兹的回路速度执行控制算法,而且还有余力来处理通信,为主机微处理器上的用户接口应用提供数据。此外,FPGA还具有可重构性,因此客户能随时根据需要调整控制算法。
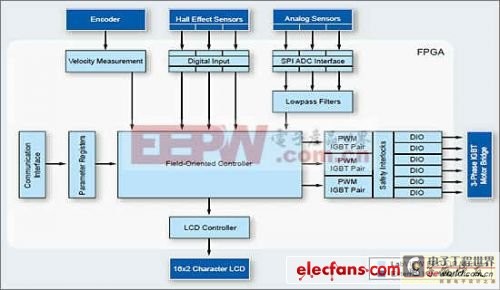
图3所示为FOC实施方案的系统图。除实际控制算法之外,FPGA还并行执行IP模块,以读取3个霍尔效应传感器、1个编码器以及3个其它模拟传感器的值,同时生成PWM信号驱动外部电子器件给电机供电。如欲与主机处理器及简单用户接口通信,可并行执行其他IP模块。
图4所示为基于FPGA的FOC算法实施LabVIEW FPGA的情况。Clarke变换将120°相移三轴坐标系(Ia, Ib, Ic)转变为两轴直角坐标系(Ia, Ib)。接着,Park变换将固定的坐标系(Ia, Ib)转换为去耦两轴旋转坐标系(Id和Iq),简单的PI控制器就能控制上述旋转坐标。FOC系统利用逆变换(Park变换和Clarke变换)将其还原到定子线圈的固定AC三相坐标系。
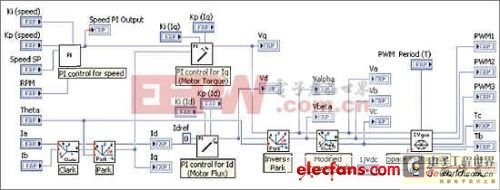
图4 基于FPGA的FOC算法实施LabVIEW FPGA的情况
在评估控制系统的升级时,机械设计人员通常会低估耗电成本问题,而从机电的整个生命周期角度来看,耗电成本往往比硬件购置成本高很多。NI致力于借助基于赛灵思FPGA技术的商用硬件解决方案成品推出具有高计算性能的高灵活性嵌入式控制器。通过二者的强强联合,能满足客户最苛刻的要求,即FOC性能要求。